Welding is a process used to combine two or more pieces of metal. It’s an essential skill in many industries, and it’s important to understand the different types of Welding available.
In this post, we’ll explore Different Types of Welding and see what each type offers.
We’ll provide an overview of the various techniques, tools, and processes you’ll need to know to become a welding expert.
So, whether you’re just starting with Welding or an experienced welder, this guide will help you stay updated with the different welding trends.
1. Flux-cored Arc Welding
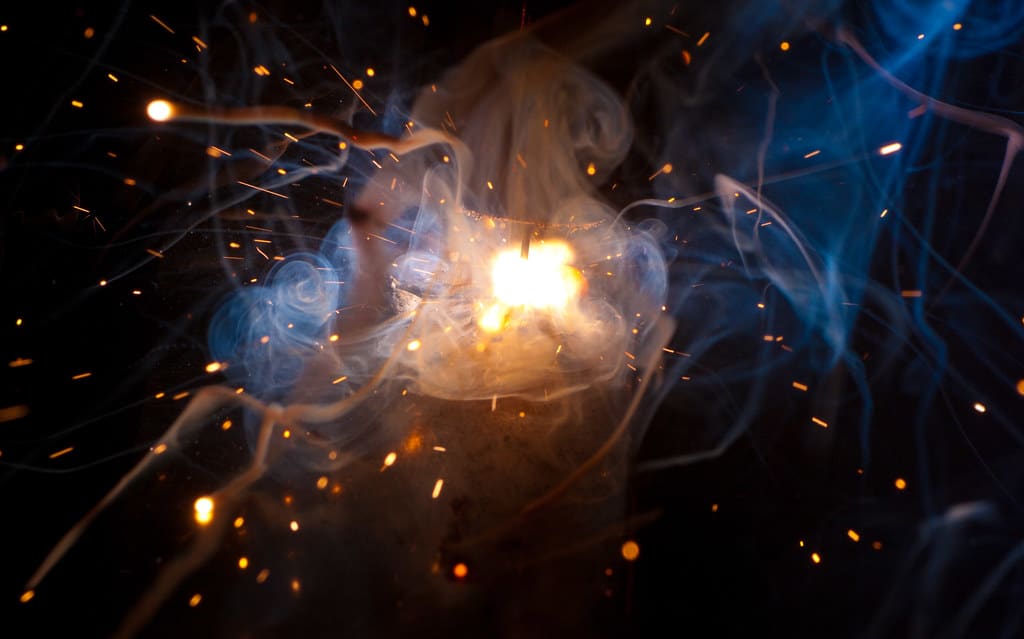
Flux-cored arc welding (FCAW) is a versatile welding technique widely used in various industries.
It falls under the Different Types of Welding category and offers several advantages over other welding methods.
One of the critical advantages of FCAW is its ability to weld thicker materials, making it suitable for heavy-duty applications.
This is due to the continuous electrode feed and a flux-cored wire, which creates a shielding gas to protect the weld pool.
Another benefit of FCAW is its high deposition rate, which means it can quickly lay down a large amount of welded metal.
This makes it an efficient choice for projects that require quick turnaround times.
FCAW is also known for its ability to produce high-quality welds with good penetration and robust mechanical properties.
The flux-cored wire allows for better welding process control, resulting in less spatter and cleaner welds.
Furthermore, FCAW is a versatile welding technique used in various positions, including flat, horizontal, vertical, and overhead.
This makes it suitable for various applications, from construction and fabrication to automotive and shipbuilding.
In summary, flux-cored arc welding is a highly versatile welding method that offers many advantages.
Its ability to weld thicker materials, high deposition rate, and production of high-quality welds make it a popular choice in different industries.
Whether you’re a beginner or an experienced welder, FCAW is a technique worth exploring.
2. Stick – Shielded Metal Arc Welding
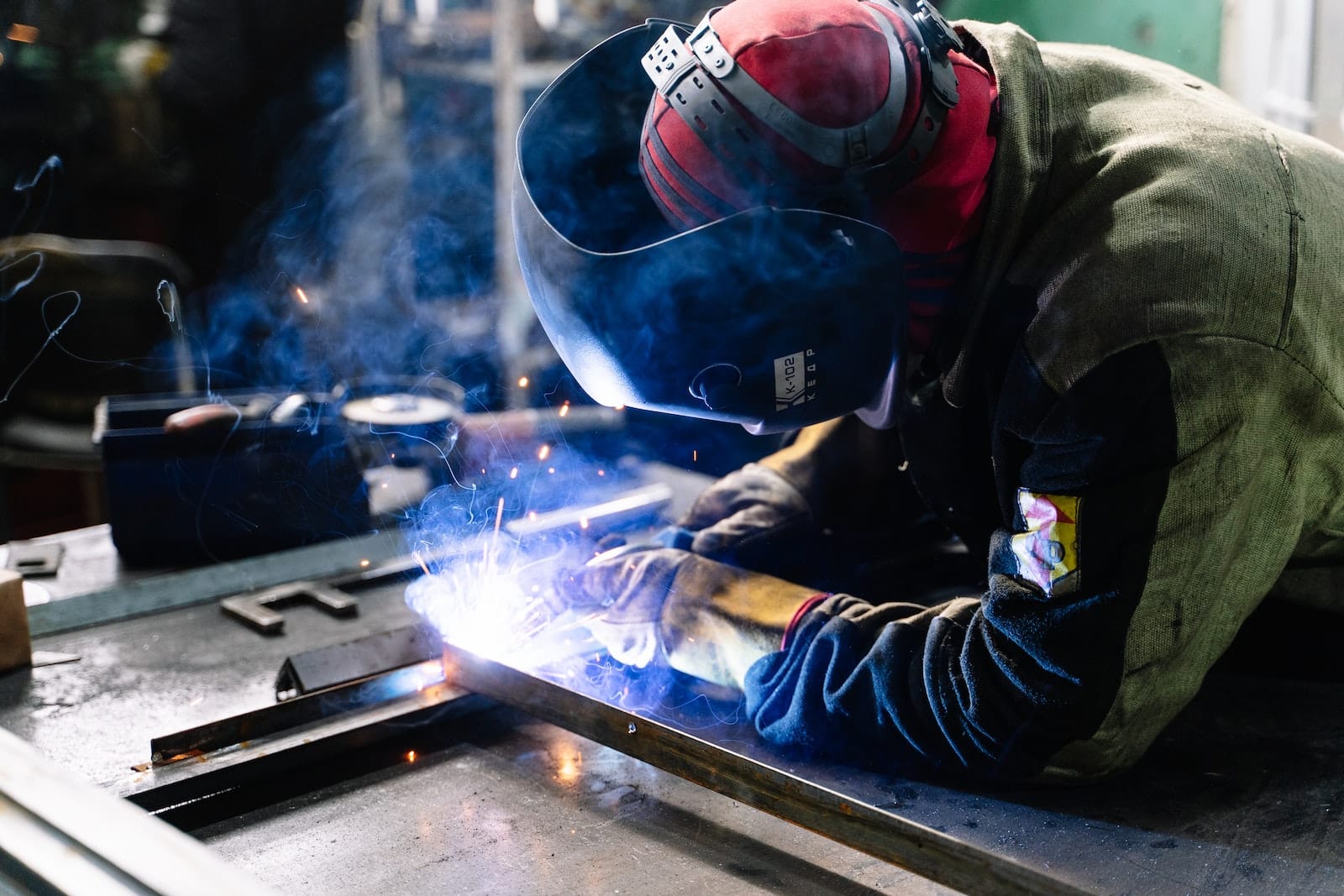
Stick Welding, also known as Shielded Metal Arc Welding (SMAW), is a widely used technique that offers versatility and reliability.
It is one of the most common types of Welding and is suitable for various applications, including construction, fabrication, and repairs. Ian electrode or “stick” is used as the filler material in stick welding.
This electrode is coated with a heat flux that releases gases, creating a shielding gas to protect the weld pool from atmospheric contaminants.
This process provides excellent control over welding, allowing for high-quality welds. One of the advantages of stick welding is its ability to work well in outdoor and remote locations.
It can be used in windy conditions or on dirty and rusty surfaces, making it a preferred choice for construction sites and field repairs.
Stick welding is also versatile regarding material compatibility, as it can be used to weld various metals, including carbon steel, stainless steel, and cast iron.
Another advantage of stick welding is its portability. It does not require external shielding gas, making it a convenient option for on-the-go projects.
The equipment used in stick welding is relatively simple and affordable, making it accessible to professionals and hobbyists.
However, stick welding does have its limitations. It can be slower than other welding techniques, as each electrode has a limited length and must be replaced frequently.
Additionally, achieving high-quality welds requires more skill and practice, as the operator needs to maintain the correct arc length and manipulate the electrode.
Stick welding, or Shielded Metal Arc Welding (SMAW), is a versatile and reliable technique.
It offers portability, compatibility with various materials, and the ability to work in challenging environments.
While it requires more skill and practice, stick welding remains prevalent in many industries.
3. Gas Welding/oxyacetylene Welding
Gas welding These different types of welding, also known as oxyacetylene Welding, is a versatile and widely used technique.
It involves using a fuel gas, typically acetylene, and oxygen, to create a flame that melts and fuses the workpieces.
Gas welding has been used for many years and is still commonly used today for various applications.
One of the advantages of gas welding is its versatility in terms of the materials that can be welded.
It can weld various metals, including steel, cast iron, aluminum, and copper. This makes it a preferred choice for repairs and fabrication in the automotive, plumbing, and metalworking industries.
Gas welding also offers excellent control over the heat input, allowing for precise and accurate Welding.
The flame temperature can be easily adjusted by controlling the flow of oxygen and acetylene, making it suitable for welding thin materials.
Additionally, gas welding is portable and does not require electricity, making it ideal for outdoor and remote welding jobs.
It can be used when limited or unavailable power sources, such as at construction sites or field repairs.
However, gas welding does have some limitations. It produces a relatively low heat output compared to other welding methods, which may limit its use for thick materials.
It also requires a high level of skill and practice to master, as the operator needs to maintain the correct flame balance and control the welding speed.
In summary, gas welding or oxyacetylene welding is a versatile welding technique that offers excellent control and versatility in material compatibility.
It is a preferred choice for various applications, particularly in outdoor and remote locations. While it requires skill and practice, gas welding remains essential for welders in many industries.
4. Forge Welding
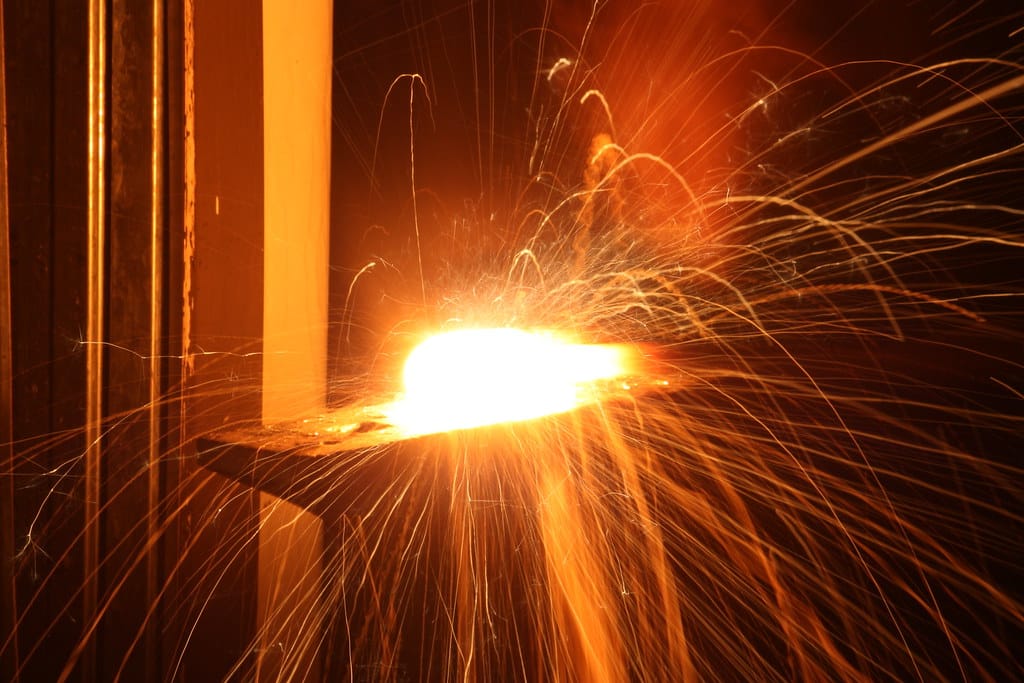
Forge Welding is one of the oldest and most traditional welding techniques. It involves heating two metal pieces until red-hot and hammering or pressing them together to form a bond.
Unlike other welding methods that use filler materials, forge welding relies on heat and pressure to create a solid joint.
Forge Welding is often used for joining metals such as iron and steel, and it is commonly used in blacksmithing and traditional metalworking.
It requires a forge or a specialized furnace to heat the metal pieces to the necessary temperature.
The process requires skill and precision, as the blacksmith needs to carefully control the heat and ensure proper alignment of the metal pieces.
One of the advantages of forge welding is its ability to create strong and durable bonds.
The high heat and pressure applied during the process allow the metal to fuse, resulting in a solid joint capable of withstanding heavy loads and stress.
Forge Welding also enables the joining of different types of metals, making it a versatile technique.
However, forge Welding does have some limitations. It requires a high level of skill and experience to perform correctly, as the blacksmith needs to judge the temperature and timing to achieve a successful weld.
It also requires a specialized setup and equipment, which may not be readily available to everyone.
In summary, forge welding is a traditional and reliable metal joining method. Its ability to create strong and durable bonds makes it suitable for various applications in blacksmithing and metalworking.
While it requires skill and specialized equipment, forge welding is an essential technique in Different Types of Welding.
5. Atomic Hydrogen Welding
Atomic hydrogen welding is a specialized technique that utilizes a hydrogen gas flame to create high-intensity heat for joining metal pieces.
It is commonly used in industries such as aerospace and nuclear power.
One of the main advantages of atomic hydrogen welding is its ability to produce solid and high-quality welds.
The high heat generated by the hydrogen flame allows for deep penetration and fusion of the metal, resulting in durable and reliable weld joints.
This makes it suitable for applications that require exceptional strength and structural integrity.
Another benefit of atomic hydrogen welding is its ability to weld various materials, including stainless steel, nickel alloys, and refractory metals.
It is particularly effective for welding thin materials and dissimilar metals, making it a versatile technique in Different Types of Welding.
However, atomic hydrogen welding does have some limitations. It requires strict control of the welding environment to prevent contamination, as hydrogen is highly reactive and can react with impurities in the metal.
Additionally, the equipment and setup for atomic hydrogen welding are specialized and may not be readily available.
In summary, nuclear hydrogen welding is a specialized welding technique that offers strong welds and versatility in material compatibility.
While it requires careful control and technical equipment, it remains an essential technique in industries that require exceptional strength and precision welding.
6. Plasma Arc Welding
Plasma Arc Welding (PAW)These different types of Welding are advanced and precise welding techniques that use a concentrated and high-temperature plasma arc to join metal pieces together.
It is commonly used in the aerospace, automotive, and electronics industries. A plasma torch creates an electric arc between an electrode and the workpiece in plasma arc welding.
The electric arc passes through a high-velocity stream of ionized gas, known as plasma, which reaches temperatures of up to 30,000 degrees Celsius (54,000 degrees Fahrenheit).
This intense heat melts the metal, allowing it to fuse and form a strong bond. One of the main advantages of plasma arc welding is its ability to produce clean and precise welds.
The narrow and focused arc allows precise control over the heat input and weld pool, resulting in minimal distortion and excellent aesthetics.
PAW also offers versatility in terms of material compatibility. It can weld various metals, including stainless steel, aluminum, titanium, and more.
Additionally, it can be used for both thin and thick materials, making it suitable for a wide range of applications.
However, plasma arc welding does have some limitations. It requires specialized equipment, including a plasma torch and gas supply system.
The process also produces significant amounts of ultraviolet radiation, requiring proper safety precautions such as protective clothing and shielding.
In summary, plasma arc welding is an advanced and precise technique offering clean and accurate welds.
Its versatility in material compatibility and ability to work with various thicknesses make it a popular choice in industries that require high accuracy and aesthetics.
While it requires specialized equipment and safety measures, plasma arc welding is an effective and reliable method for joining metals.
7. MIG – Gas Metal Arc Welding
MIG, or Gas Metal Arc Welding (GMAW), is a widely used welding technique that offers versatility and ease of use.
It is commonly used in various industries, including automotive, manufacturing, and fabrication. One of the main advantages of MIG welding is its high welding speed.
It uses a continuous solid wire electrode fed through a welding gun and shielding gas.
This allows for quick and efficient Welding, making it ideal for projects that require high productivity.
MIG welding also offers excellent control over the weld pool and the ability to weld various materials, including carbon steel, stainless steel, aluminum, and more.
The shielding gas used in MIG welding protects the weld pool from atmospheric contamination, resulting in clean and strong welds.
Another benefit of MIG welding is its versatility in terms of welding positions. It can be used in various places, including flat, horizontal, vertical, and overhead.
This makes it suitable for various applications, from thin sheet metal welding to heavy-duty structural Welding.
Additionally, MIG welding is relatively easy to learn and operate, making it accessible to beginners and hobbyists.
The equipment used in MIG welding is also affordable and readily available, making it a popular choice for both professionals and DIY enthusiasts.
In summary, MIG or Gas Metal Arc Welding is a versatile and efficient welding technique that offers high welding speed, excellent control, and compatibility with a wide range of materials.
Its ease of use and accessibility make it a popular choice in many industries.
8. Electron Beam Welding
Electron Beam Welding (EBW) is another different types of welding, an exact and advanced welding technique that utilizes a focused beam of high-energy electrons to join metal pieces.
It is commonly used in the aerospace, automotive, and medical device manufacturing industries.EBW offers several advantages over other types of Welding.
One of the key benefits is its ability to create deep and narrow welds with minimal distortion.
The focused electron beam provides precise heat input, allowing precise control over the weld pool.
This makes EBW suitable for applications that require high accuracy and minimal heat-affected zones.
Another advantage of EBW is its ability to weld a wide range of materials, including metals with different melting points and dissimilar metals.
It can create strong and durable bonds between traditionally difficult materials to fuse, making it a valuable technique in fabricating complex components.
Additionally, EBW offers a high degree of automation, making it suitable for high-volume production.
It can be easily integrated into robotic systems, reducing the need for manual labor and improving efficiency.
However, EBW does have some limitations. It requires expensive and specialized equipment, including a vacuum chamber, to maintain the environment needed.
Additionally, the process is sensitive to surface contaminants and requires careful preparation to ensure successful welds.
In summary, Electron Beam Welding is a precise and advanced welding technique that offers excellent control, versatility, and automation.
It is a preferred choice in industries that require high accuracy and complex welding applications.
While it requires specialized equipment and expertise, EBW remains essential to Different Types of Welding.
9. Resistance Welding
Welding is a fascinating and essential skill in various industries. There are many types of welding techniques, each offering advantages and applications.
In this guide, we’ll provide an overview of the different kinds of Welding and what they entail.
First, we have flux-cored arc welding (FCAW), known for its versatility and ability to weld thicker materials.
It has a high deposition rate and produces high-quality welds, making it a popular choice in heavy-duty applications. Next, we have stick welding or Shielded Metal Arc Welding (SMAW).
It is a widely used technique suitable for various applications and offers versatility regarding material compatibility. It is known for its portability and affordability.
Gas welding, also known as oxyacetylene Welding, is another versatile technique that can be used to weld various metals.
It offers excellent control over the heat input and is portable, making it ideal for outdoor and remote locations.
Forge Welding is a traditional technique that uses heat and pressure to create a solid joint.
It is commonly used in blacksmithing and metalworking and is known for its strength and durability.
10. Thermit Welding
Thermit welding, also known as thermite or exothermic Welding, is a unique welding process primarily used to join rail tracks, electrical conductors, and other similar applications.
It is a fusion welding technique that relies on a chemical reaction to generate heat for Welding.
Thermit welding combines a powdered metal alloy called thermit with a metal oxide, typically iron oxide.
When ignited, the thermit reaction produces intense heat, reaching around 2,500 degrees Celsius (4,500 degrees Fahrenheit). This heat is sufficient to melt the metal, allowing it to fuse and form a strong bond.
One of the main advantages of thermit welding is its ability to create permanent and durable connections.
The resulting weld has excellent mechanical properties, high strength, and good fatigue resistance.
It also provides superior electrical conductivity, making it suitable for electrical applications—thermit welding benefits applications where traditional welding techniques are not practical or feasible.
It can join different types of metals, including steel, copper, and aluminum. Additionally, it is effective in joining thick sections or dissimilar materials.
However, thermit welding does have some limitations. It is a specialized process that requires skilled operators and specific equipment.
The equipment used for thermit weldings, such as the mold and crucible, is typically one-time use, which adds to the overall cost of the process.
In summary, thermit welding is a unique and specialized technique that uses a chemical reaction to generate heat for fusion welding.
It offers robust and durable connections, making it suitable for specific applications such as rail tracks and electrical conductors.
While it requires specialized knowledge and equipment, thermit welding is an effective and reliable method for joining metals.
11. Tig–Gas Tungsten Arc Welding
TIG, or Gas Tungsten Arc Welding (GTAW), These different types of welding is a precise and versatile welding technique commonly used in aerospace, automotive, and fabrication industries.
If needed, TIG welding uses a non-consumable tungsten electrode to produce the weld and a separate filler material.
One of the main advantages of TIG welding is its ability to create high-quality, clean welds.
The TIG process allows precise control over the heat input and weld pool, resulting in minimal distortion and excellent aesthetics.
It also offers a wide range of material compatibility, including stainless steel, aluminum, and titanium.
TIG welding is particularly well-suited for thin materials, as it produces a concentrated arc that allows for precise control over the weld bead.
This makes it ideal for applications that require intricate and detailed welds, such as pipe welding and ornamental metalwork.
Additionally, TIG welding offers versatility in welding positions, including flat, horizontal, vertical, and overhead.
It can be used for manual and automated Welding, making it suitable for various projects.
However, TIG welding these types of welding has a higher skill requirement than other welding techniques.
The welder must have a steady hand, good coordination, and knowledge of the welding parameters to achieve optimal results.
In summary, TIG or Gas Tungsten Arc Welding is a precise and versatile welding technique that offers high-quality, clean welds.
Its ability to work with various materials and perform intricate welds makes it a popular choice in industries that require precision and aesthetics.
While it requires skill and practice, TIG welding is essential for welders looking to expand their capabilities.
12. Submerged Arc Welding
Submerged arc welding (SAW) is a welding process that uses a granular flux to protect the weld pool from atmospheric contamination.
It is commonly used in shipbuilding, construction, and oil and gas pipelines.
In submerged arc welding, the electrode is a continuous wire fed into the weld zone and a flux layer.
The flux is granular and is deposited around the weld to create a protective blanket. The heat generated by an electric arc melts the electrode, change, and workpiece, forming a molten weld pool.
The difference also acts as a slag, solidifying and protecting the weld as it cools.
One of the advantages of submerged arc welding is its ability to produce high-quality welds with excellent penetration and fusion. The flux provides a clean and smooth weld bead with minimal spatter and slag. This makes SAW suitable for welding thick materials and significant structural components.
Another benefit of submerged arc welding is its high deposition rate. It can quickly lay down large amounts of welded metal, making it efficient for high-volume production.
Additionally, SAW is a highly mechanized process, often used with automatic or semi-automatic systems, which increases productivity and reduces labor costs.
However, submerged arc welding does have some limitations. It requires a clean workpiece surface, as the flux cannot effectively protect against contaminants.
The process also produces significant heat and smoke, requiring adequate ventilation and safety measures.
In summary, submerged arc welding is a versatile and efficient technique offering high-quality welds and high deposition rates.
It is commonly used in heavy industries and is well-suited for welding thick materials and large structures.
While it requires proper safety precautions and surface preparation, submerged arc welding is an effective method for joining metals.
Conclusion
In this post, we explored the different types of Welding and delved into what each type offers.
Each technique has unique advantages and applications, from flux-cored arc welding to TIG welding.
These types of Welding are essential skills to have in many industries, and understanding the strengths and limitations of each type is crucial for welders.
Flux-cored arc welding offers versatility and the ability to weld thicker materials, while stick welding is known for its portability and compatibility with various metals.
Gas welding provides excellent control and is ideal for outdoor and remote locations.
Forge Welding relies on heat and pressure to create solid and durable bonds, while atomic hydrogen welding offers exceptional strength and versatility in material compatibility.
MIG welding is known for its high welding speed and compatibility with a wide range of materials, and electron beam welding offers precise control and automation.
Resistance welding is commonly used for high-volume production, and thermit welding is a unique process for specific applications.
TIG welding is accurate and well-suited for thin materials and intricate welds, while submerged arc welding is efficient for welding thick materials and large structures.
By understanding the types of Welding and their specific uses, welders can choose the proper technique for their projects, ensuring high-quality and reliable welds.
Whether you’re just starting or an experienced welder, knowing the different types of Welding will help you stay up to date with the latest trends in the industry.
So, get out there and start exploring the world of Welding!